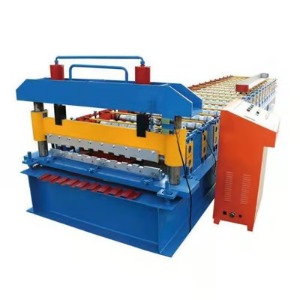
Highly efficient metal roll forming
We provide free samples, you just need to cover the shipping cost. We sincerely look forward to cooperating with you for mutual benefit, and please contact us for any other questions.
Original Design Manufacturer
Manufacturing of metal cold forming equipment
One-stop sales and support services
Metal Roll Forming
Introduction:
Metal roll forming is a highly efficient and versatile manufacturing process used to create complex metal profiles with consistent cross-sections. This innovative technique involves feeding a metal strip or coil through a series of rollers, gradually shaping it into the desired form. With its precision and flexibility, metal roll forming offers numerous advantages for various industries, including construction, automotive, and appliance manufacturing.
Section 1: High Precision and Consistency
With metal roll forming, manufacturers can achieve exceptional precision and consistency in the production of metal profiles. The process involves passing the metal strip through multiple sets of rollers, each carefully designed to shape and form the material. This ensures that each product has the same dimensions, tolerances, and surface finish, meeting the most stringent quality standards. Whether it's a simple angle or a complex structural shape, metal roll forming guarantees consistent results every time.
Section 2: Versatile Range of Shapes and Sizes
Metal roll forming offers an extensive range of possibilities when it comes to creating different shapes and sizes. The flexibility of the process allows manufacturers to produce profiles with various cross-sections, including angles, channels, tubes, and custom designs. This versatility makes metal roll forming an ideal choice for a wide range of applications, from architectural elements to automotive components. The ability to customize profiles to meet specific requirements is a significant advantage of this manufacturing technique.
Section 3: Cost-Effective Production
When compared to other metal forming methods, metal roll forming offers significant cost savings. The process is highly efficient, with minimal material waste and reduced labor requirements. The continuous nature of roll forming allows for high-volume production, resulting in economies of scale. Additionally, the use of pre-painted or pre-coated metal strips eliminates the need for additional surface treatment, further reducing costs. Metal roll forming is an economical solution for manufacturers looking to optimize their production processes.
Section 4: Strength and Durability
Metal roll forming produces profiles with excellent strength and durability. The continuous bending and shaping of the metal strip enhance its structural integrity, making it suitable for demanding applications. The uniformity of the material distribution along the profile ensures consistent strength and prevents weak points. Additionally, the option to use high-strength alloys further enhances the durability of the final product. Whether it's for load-bearing structures or protective barriers, metal roll-formed profiles offer reliable performance.
Section 5: Enhanced Design Flexibility
One of the key advantages of metal roll forming is its ability to provide enhanced design flexibility. Manufacturers can create complex profiles with intricate shapes and patterns, allowing for unique and visually appealing products. The process enables the integration of features such as embossing, perforations, and cutouts, opening up a world of design possibilities. Whether it's achieving aesthetic appeal or incorporating functional elements, metal roll forming empowers designers to push the boundaries of creativity.
Section 6: Fast and Efficient Production
Metal roll forming offers fast and efficient production capabilities, enabling manufacturers to meet tight deadlines and high demand. The continuous nature of the process allows for rapid production rates, ensuring a steady supply of finished products. The automated nature of roll forming equipment further enhances efficiency, reducing the need for manual labor and minimizing downtime. With metal roll forming, manufacturers can streamline their production processes and optimize productivity.
Section 7: Excellent Material Utilization
Material utilization is a crucial aspect of any manufacturing process, and metal roll forming excels in this regard. The continuous nature of the process minimizes material waste, as each section of the metal strip is utilized efficiently. Additionally, manufacturers can optimize the nesting of profiles, maximizing the number of parts that can be obtained from a single strip. This efficient use of materials not only reduces costs but also has a positive impact on the environment by minimizing scrap generation.
Section 8: Consistent Surface Finish
Metal roll forming ensures a consistent surface finish across the entire length of the profile. As the metal strip passes through the rollers, any imperfections or surface irregularities are smoothed out, resulting in a uniform appearance. This is particularly important for visible applications where aesthetics play a crucial role. Whether it's a polished, painted, or coated finish, metal roll forming guarantees a consistent surface quality that enhances the overall product's visual appeal.
Section 9: Quick and Easy Assembly
Thanks to its precise dimensions and consistent cross-sections, metal roll-formed profiles offer quick and easy assembly. The accurately formed features, such as tabs, flanges, and interlocking mechanisms, ensure a seamless fit during the assembly process. This reduces the need for additional machining or modifications, saving time and effort. Whether it's on-site construction or assembly line production, metal roll-formed profiles facilitate efficient and hassle-free installation.
Section 10: Longevity and Low Maintenance
Metal roll-formed profiles are known for their longevity and low maintenance requirements. The inherent strength and durability of the material, coupled with the precise shaping process, result in products that can withstand harsh conditions and heavy loads. Metal roll-formed profiles are resistant to corrosion, impact, and wear, reducing the need for frequent repairs or replacements. This makes them a cost-effective choice in the long run, saving both time and resources.